Step 1: Harvest the logs
For Vietnamese plywood, input materials usually include common woods like acacia, eucalyptus, and rubber. Workers harvest logs with a diameter over 12 cm from planted forests and cut them into pieces of standard sizes.
Step 2: Peel and slice the wood from logs
Freshly harvested wood goes through preliminary processing. First, workers remove the outer shell. Then, a specialized machine creates thin wooden panels, each about 1.7mm to 2mm thick. The machine peels the core veneer from the outside towards the center until the log is fully used. The cutter must have a sharp blade to ensure even thickness and avoid breaking the veneer layers.
Step 3. Sorting and drying
Workers sort veneer from logs by wood type and size, removing non-standard panels.
Next, they sun-dry the boards to a moisture content of 20%-30%. They then use a machine to dry the boards further, controlling the temperature to achieve standard humidity levels.
After drying, workers classify the boards by surface quality, grading them from A to F, with A as the highest quality and F as the lowest.
Step 4: Arrange the core veneer
This stage is crucial, determining 90% of the board’s quality. Workers glue and stack layers into a long chain. They secure the joints with plastic nails. A specialized cutting machine at the end cuts the stack into standard-sized rebar plates.
Step 5. Cold press and hot press
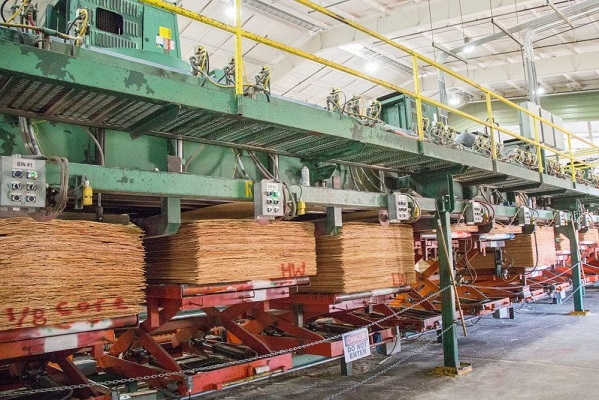
Step 6. Surface bait repair
The hot-pressed core veneer continues to be repaired for the second time, the surface bait to ensure aesthetics as well as quality.
After that, the bait must be allowed to cool down to continue the next processing stage
Step 7. Sanding
The core veneer is fed into a specialized machine for sanding in turn on both sides with a support device for automatic flipping and preliminary cutting to produce boards that are generally uniform in size.
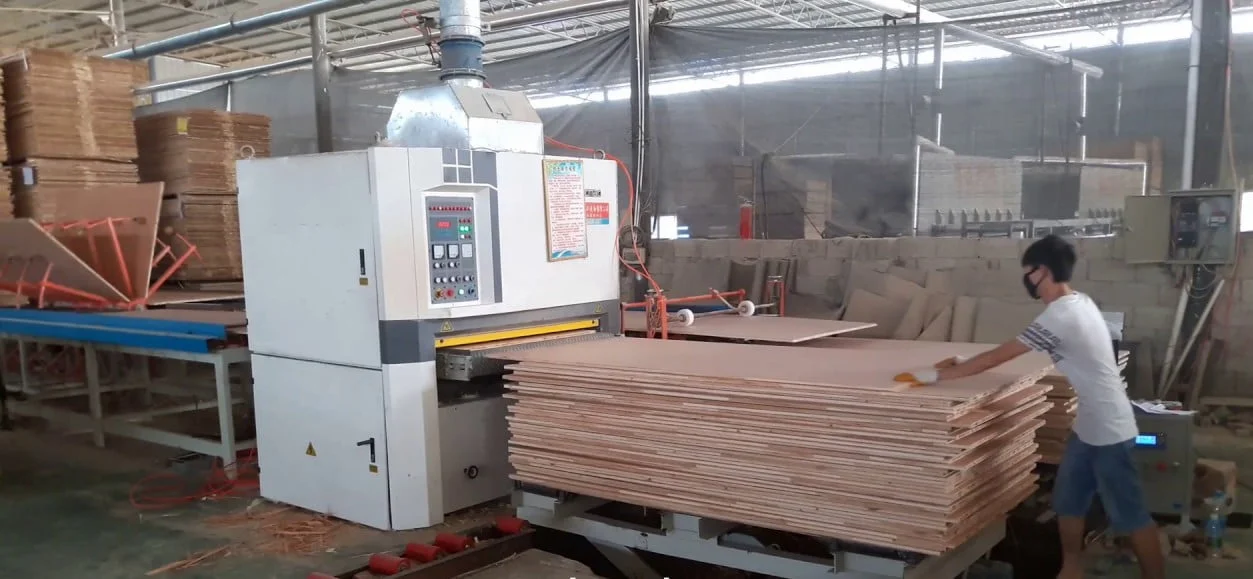
Step 8. Cold Pressing and Hot Pressing Surface
The wood panels have been coated with glue and the face will be put into cold pressing and hot pressing similar to that of core wood. These stages help the surface to bond closely with the core, as well as reinforce the adhesion between the layers of the boards. With commercial plywood, Vietnam has many types of face veneers such as: Bintangor, Okoume, Birch, Pine, …
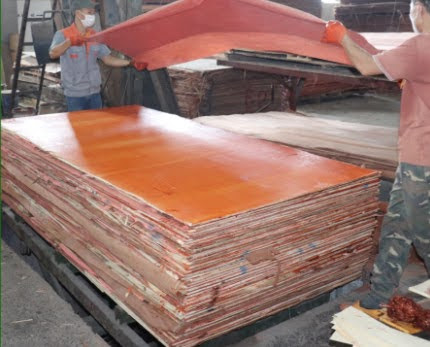
Step 9: Cut to standard size
Workers measure and cut semi-finished boards to the required size. They ensure the board surface is flat and clean. The board size must meet the standard. Workers also check that the corners are safe.
Step 10: Inspecting the goods, sanding the edges of the board and packing
After face pressing will be re-checked:
-Core quality: use a hammer to knock again to see if the board is smashed
-Face quality: Is the surface flat and beautiful or is there a problem of fraying, glue seepage?
-Use a hand scrubber to sand the edges of the board to make it more beautiful.
Plywood that does not meet the quality required by customers will be rejected. The goods will be packed with pallets and sturdy bales before being loaded onto the cart and sent to the customer.