Plywood manufacturing can have various defects that affect the quality and usability of the final product. These defects can occur in the core or on the surfaces of the plywood. Here, we explore common problems and defects found in plywood manufacturing.
1. Gluing Defects
1.1 Weak Bonding
Weak bonding in plywood indicates that the bonding strength is below the standard value. Causes include:
- Poor adhesive quality
- Inadequate control of hot pressing conditions (e.g., low temperature, insufficient pressure, short pressing time)
- Low veneer moisture content
- Insufficient glue application
- Poor veneer quality
- Improper aging time
1.2 Bubbling or Delamination
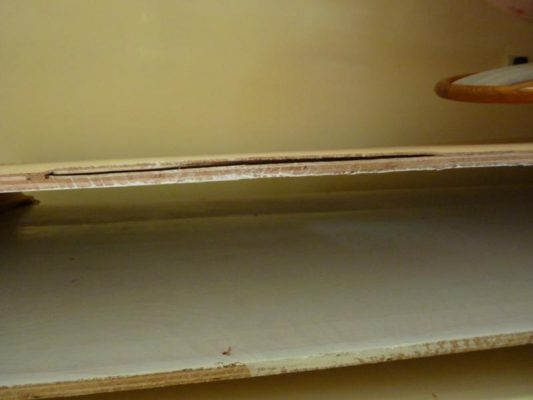
Bubbling occurs when steam trapped in veneer gaps creates raised bubbles on the surface during pressure reduction, often with a loud sound. Delamination, where the plywood layers separate, may occur simultaneously. Causes include:
- Rapid pressure drop
- Insufficient hot pressing time
- High veneer moisture content
- Excessive glue application
- Veneer imperfections or inclusions during glue application
- Poor air permeability in pine plywood
- Excessive hot pressing temperature
1.3 Delamination at corners
Corner delamination happens when the corners of the plywood are not glued properly, leading to splits. Causes include:
- Veneer drying before hot pressing
- Lack of glue at corners
- Poor glue quality and bonding strength
- Uneven veneer thickness
- Misalignment of slabs during assembly
- Worn pressing plate corners
- Insufficient pressure and uneven pressing plate temperature
2. Structure Defects
2.1 Plywood warping
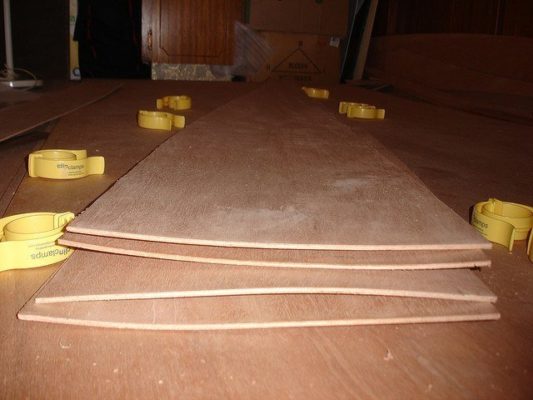
Warped plywood is easily noticeable when placed horizontally. Causes include:
- Inconsistent moisture content between surface and backboard
- Unreasonable veneer matching violating symmetry principles
- Veneer with torsion patterns
- Uneven hot press plate temperatures
- Uneven stacking surfaces
2.2 Core Board Separation
Core board separation manifests as stacked or separated edge strips, causing visible streaks and unevenness on the board surface. Causes include:
- Incorrect gap size during manual core discharge
- Misalignment during assembly
- Uneven parts, cracks, or ruffles
2.3 Missing Edges
Missing edges occur when the plywood’s case back and core board are insufficient in size. Causes include:
- Improper glued assembly
- Incorrect surface and back panel sizes and arrangement
- Edges of plywood getting stuck or backboard glue application issues
2.4 Too High Moisture Content
The moisture content of the board should not exceed 12%. Boards exceeding this limit should be excluded from shipments.
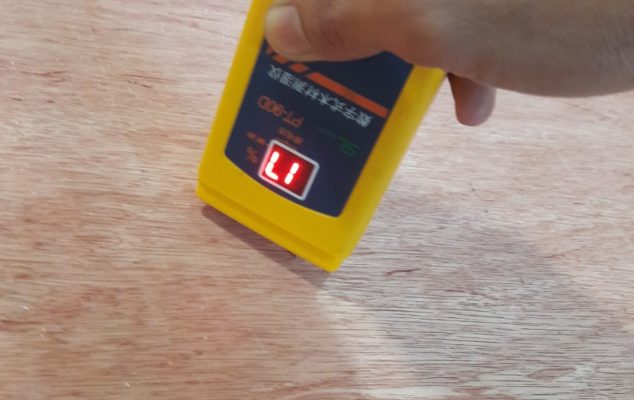
3. Appearance Defects
3.1 Adhesive Penetration
Adhesive penetration results in glue marks on the board surface. Causes include:
- Excessively thick glue
- Deep cracks on the veneer back
- High veneer moisture content
3.2 Discoloration
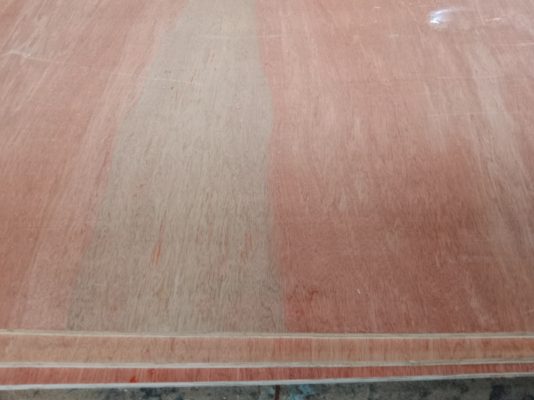
Abnormal color on the plywood surface can result from:
- Highly alkaline or acidic glue reacting with high-tannin wood
- Veneer not dried promptly in humid conditions, leading to mold
- Hot press board leaks
3.3 Face Veneer Splits

Short splits can be fixed with putty, while long splits cannot and should be rejected.
3.4 Face Veneer Delamination
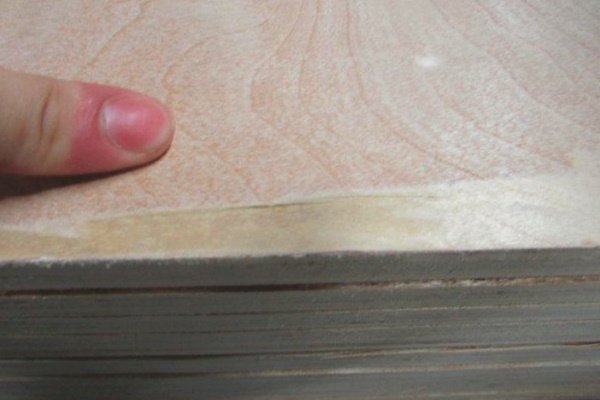
Face veneer delamination indicates the separation of veneer layers.
Conclusion
Quality control processes in plywood manufacturing play a crucial role in identifying and addressing these defects. A comprehensive quality control system involves regular inspections and testing at various stages of production to detect issues early. This proactive approach helps in minimizing defects and ensuring that any problematic boards are either fixed or rejected before they reach the market.
Inspectors should meticulously check for gluing, structural, and appearance defects. For gluing defects, they need to monitor bonding strength and look for signs of bubbling or delamination. Structural defects such as warping, core board separation, and missing edges should be carefully examined to maintain the board’s integrity. Appearance defects like adhesive penetration, discoloration, and face veneer splits require thorough visual inspections to ensure the plywood meets aesthetic standards.